Anodizing knowledge
We started out in an attic.
Keywords:
The name Eloxal and Anodizing
The name ELOXAL is a German made-up word and is composed of ELektrolytische OXidation des ALuminiums (ANODYLYTIC OXIDATION of ALUMINIUM), which explains that it only works with aluminum. Anodizing describes the process of anodizing aluminum, but anodizing in general can also be applied to other materials. So you can use both terms for this material!
Choice of material
A wide range of different alloys are available on the market today. However, the “jack of all trades” has not yet been invented, so a compromise must always be made between the various properties. This applies to machinability, strength, price, and even decorative anodizability. If, for example, the focus is on a perfect surface finish, only certain low-alloy materials can be used (AlMgSi0.5/1, AlMg1/3 etc.). Since the wrong choice of material can mean that the end result can no longer be achieved, it is very important to make the right decision at the outset. Use our material recommendation for this purpose, or let us advise you directly. The topic is not easy and a layman can hardly filter out the optimal solution for his application from all the alloys and different brand names on the market. This is our day-to-day business!
Degreasing
Pickling
The following possible chemical pretreatments are pickling and brightening. Both processes remove material and affect the dimensional accuracy. The alloy and the material quality also have a significant influence on this. For example, a real matt finish can never be achieved on the aluminum of precision mechanical products by pickling, since this would require a very long pickling time, which would then ruin all fits. A decorative anodizing finish (EQ =Eloxal Quality) is only achieved with the few truly suitable alloys. In the case of structural problems such as coarse grain or pseudo coarse grain, the pickling process even brings out these defects – so they only become visible after pickling. We use a very short standard pickling process, which cleans the surface again and compensates for the subsequent layer structure. Many items are not pickled at all. Often, customers request a pickling process according to E6, a standard term used in architectural anodizing. If we were to follow this specification, the components would usually be destroyed immediately. Typical E6 pickling times are 20 minutes – the change in diameter would then be approx. 80-100 µm! If a matt finish is desired, it often makes the most sense to sandblast in advance. If possible, we work in an automatic system and only use stainless steel blasting material. Otherwise, we also have three high-quality pressure blasting cabinets with different grain sizes.
Chemical brightening
Another possibility is Chemical brightening. This is a chemical pretreatment and not a special type of anodizing, so it is not actually gloss anodizing. We work with a chemical brightening process in our company and are therefore limited to alloys with a maximum copper content of 0.5%. Since the brightening process is simple to execute, the alloy itself has a decisive influence on the degree of gloss achieved. This process is relatively expensive because the acid mixture used works at 100°C and a large amount is required. The result is a silky gloss that significantly enhances the appearance. This process step is particularly interesting in combination with the upstream blasting. This rounds off the pointed structures of the blasted surface, creating a great feel and making the surfaces very resistant to fingerprints and abrasion. A good example of this are the very fine surfaces from Apple, although it is difficult to achieve such a perfect result with small series and individual pieces.
Anodizing
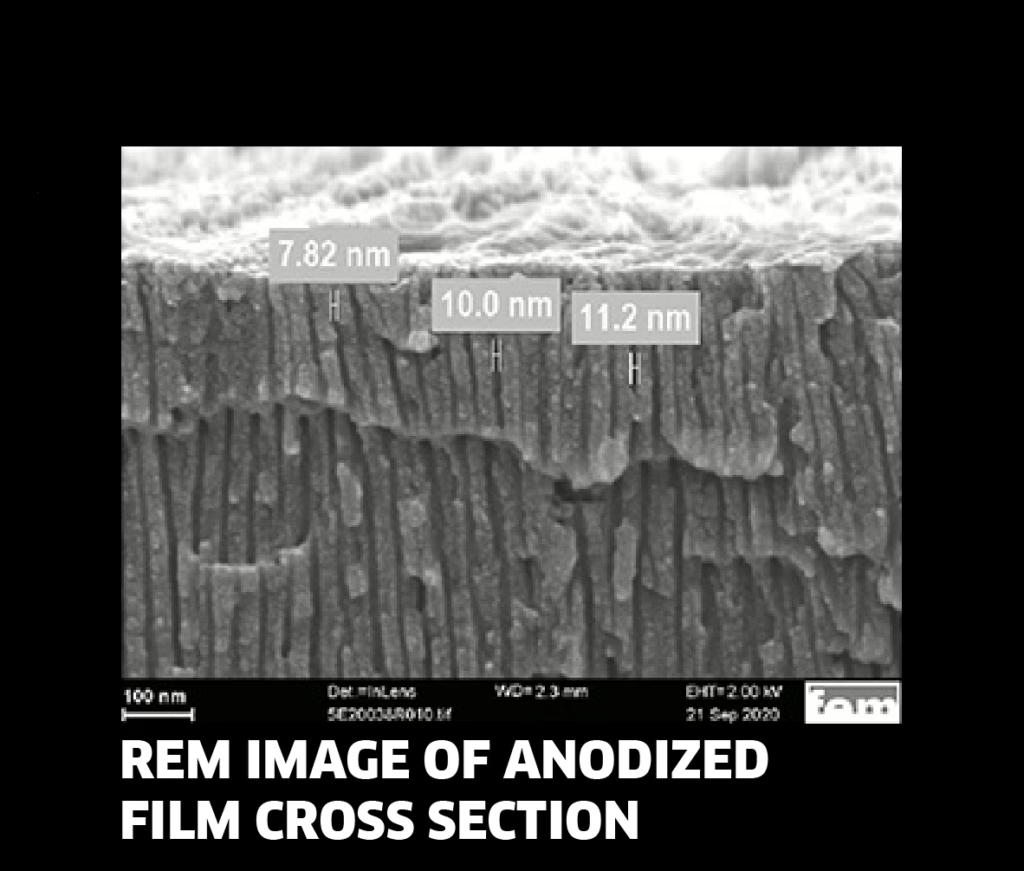
In practice, anodizing is carried out in the process sequence after the pretreatments and before the post-treatments. Almost exclusively, the GS process is used worldwide, where G stands for direct current and S for sulfuric acid. The electrolyte, i.e. the chemical bath, consists of sulfuric acid and water, sometimes with a few additives. Anodizing is done with the help of direct current, whereby the components are connected as anodes – that is why the process is also called anodizing (so + is connected here…). The temperature must be stabilized at approx. 18 °C. Since a lot of waste heat is generated, we permanently cool against the temperature increase with powerful cooling systems.
The layer that forms is always automatically silver, which is why the uncolored anodization is also called natural anodization (the term silver anodization is therefore superfluous…). The anodized layer is covered with countless pores, which are so small, however, that they cannot be seen at normal magnification (approx. 10-20 nm).
The process control during anodizing is crucial for the quality of the surface. We use our patented self-learning current density control system of the POC type for control. This system, which is unique worldwide, uses the previously learned individual current density profiles for the control processes. Typical layer thicknesses are approx. 10-15 µm for uncolored and 15-20 µm for colored anodizing. Unfortunately, only visual deficits can be detected. Deficiencies in the area of UV stability or corrosion protection are only noticed when it is too late. Therefore, the choice of a reliable and competent anodizer is the most important thing, even though there is always a cheaper one! (but this also applies to machining…)
Hard anodizing / hard anodizing / hard coat / hard coating / coating
Hard anodizing, hard anodizing, hard coat, hard coating, coating or even hard coat and hard coat (with d instead of t) ultimately all describe the same thing. It is about creating hard oxide layers. The process is very closely related to anodizing, which is why the choice of the appropriate alloy is an absolute requirement here as well. High copper contents have a dramatic disruptive effect and layers of inferior quality are obtained. In addition, there is always a very high risk of current punctures, which can even destroy the components! Slightly modified electrolytes are used, but the main difference is the lower temperature of the anodizing bath. The process usually takes place at -5 °C to 0 °C. The resulting reduced conductivity of the liquid leads to significantly higher voltages and even more heat build-up. It is crucial that the process temperature is kept constant throughout the entire hard anodizing process and the energy input is very high. The processes take up to 1 1/2 hours in this bath. The hard anodized layers are considerably harder than those of anodization. Hardness levels of up to HV550 can be achieved, and the abrasion resistance under sliding stress is often comparable to that of hard chrome layers, and sometimes even superior. However, customers often confuse hardness with abrasion resistance, which are not at all correlated. In our experience, the decisive factor is usually smoothness. This has a decisive influence on the sliding properties and wear. Often, a slightly less hard but smoother hard anodized layer is much more durable in practical use than a hard coat with maximum hardness.
Our patented polymeroxid® process produces the smoothest and most durable layers on the market, and we use it to coat tens of thousands of chassis components for renowned sports car and racing motorcycle manufacturers every year. By creating an optimized polymeroxid® matrix, we can even produce crack-free layers, which are of great interest in chassis construction, hydraulics and pneumatics. When the abrasive is smaller than 10 µm, there is always a risk of partially hitting the base material.
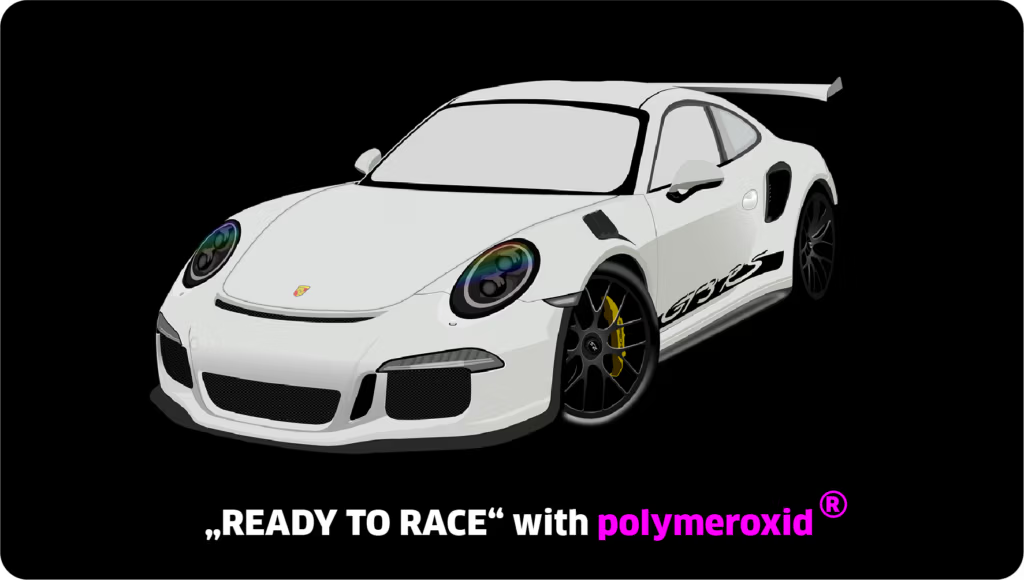
At these points, the rapidly spreading destruction of the hard coat begins. Since the hard anodization follows the electric field lines, the process only scatters into holes to a limited extent. Up to a ratio of 2.5 between depth and diameter, this can be neglected for blind holes (open on both sides 5…); beyond that, internal electrodes must be used, provided this is technically possible (e.g. hard anodizing on shock absorbers). It is correct to take the layer structure of the hard anodizing into account when calculating the mechanical processing. We always calculate with an effective build-up of 40% of the total layer thickness. A hard anodized layer with 50 µm will therefore build up approx. 20 µm per side, and then approx. 40 µm on the diameter. Compensating for this with an upstream pickling process is technically possible in theory and is also done in emergencies, but it should really only be used in emergencies.
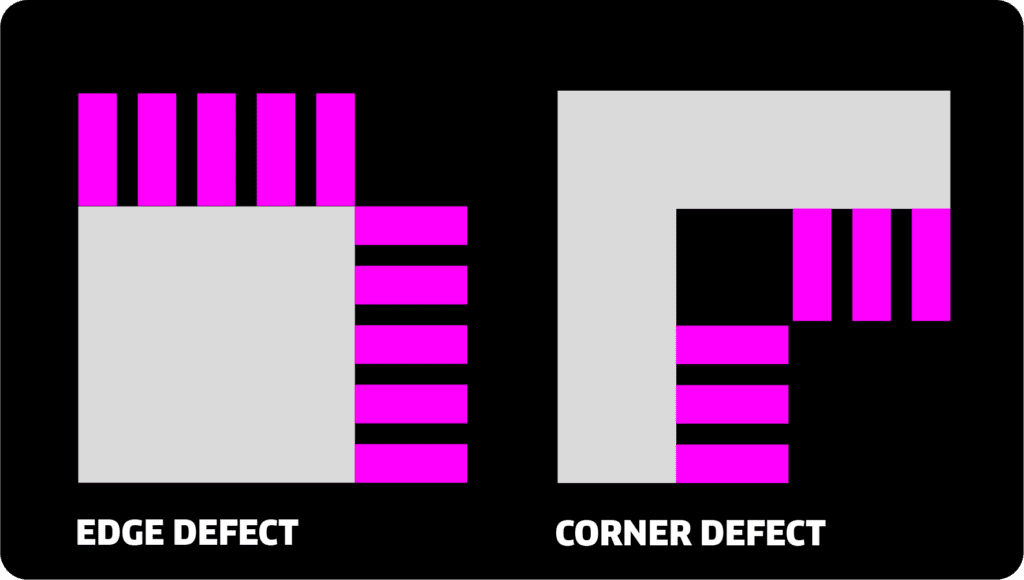
On the one hand, the hard anodizing is then naturally rough due to the pickling, which is technically complete nonsense. On the other hand, discussions are inevitable if it does not fit (pickled too long or too short!). So it often makes more sense to cover one or the other area in our company in advance, which we do in a separate department with special plugs, liquid paints or plotted stickers. Sharp edges should be avoided during hard coating, as this often causes difficulties.
Dyeing
The very small pores in anodizing or hard anodizing can be used for dyeing. In this case, color pigments are then incorporated in the anodization process in the following bath stages. The choice of suitable dye and the correct filling with the pigments is crucial for the long-term stability of the coloration. We only use dyes from TECHEVON (USA) and Clariant (CHE). A separate bath container must be provided for each color, which is why the selection of colors is limited. We use the colors red, blue, green, orange, yellow, violet, titanium and black. Special colorings are possible in principle, but they are quite expensive because a complete dye bath has to be prepared for this, which then has to be disposed of after use. The dyes, like all organic substances (including you!), are all differently temperature and UV stable. Electrolytic dyeing processes, which can be used to produce UV-stable bronze and black tones, are not applicable to the alloys commonly used in precision engineering. By using a special UV filter, we are able to guarantee acceptable UV stability even for critical colors. With color anodizing, defects in the process can be seen directly in the different color characteristics, which is why many anodizing companies experience never-ending difficulties and discussions.
In addition to the use of high-quality and homogeneous materials, only a really good and stable process control and analytics can lead to success. By using our patented polymeroxid® hard anodizing, we are able to produce useful colorings even on these dense oxide layers, which are actually considered non-dyeable. The color black is most in demand for hard anodization. We achieve an absolutely deep black and not the usual dark gray. Particularly interesting for this purpose is a special variant of hard coating – our polymeroxid® LF4.
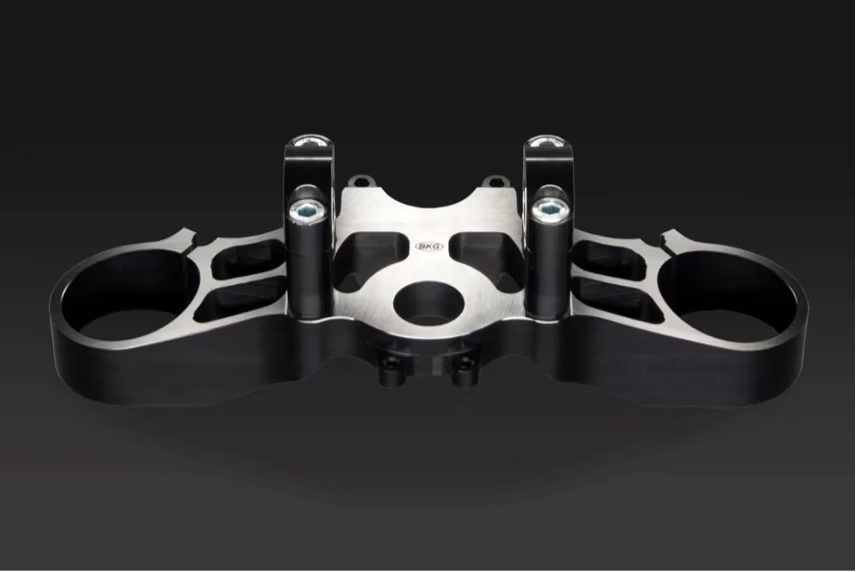
Sealing
Das Verdichten ist die letzte Stufe der Prozesskette. Eloxalschichten werden in der Regel in siedendem Wasser verdichtet. Hier verschließt man die Porenstruktur, wodurch dann der UV-Schutz und die Korrosionsstabilität erzielt wird. Möglich ist auch der Einsatz der sogenannten Kaltverdichtung, einem aus Japan stammenden energiesparenden Verfahren. Dieses hat einige technische Vorteile, ist aber aufwendig in der Prozessführung und Analytik. Wir benutzen dieses Verfahren als Standard – oft auch in der Kombination mit der Heißverdichtung. Hartcoat wird in vielen Betrieben überhaupt nicht verdichtet, da klassische Heißverdichtungen die Härte reduzieren. Wir arbeiten auch hier gerne mit dem Kaltverdichten, da die Bauteile anschließend nicht mehr empfindlich gegen Fleckenbildung durch Öle sind und auch bei Berührung nicht mehr kleben.
Finally...
Blind holes are always a major problem for anodizing and hard anodizing, and one that has yet to be solved worldwide. This applies to all areas of electroplating. Air bubbles often get caught here, preventing coating. It is therefore pure coincidence whether these spots are coated later or not. Pickling and/or electrolyte residues also tend to accumulate here, which cannot be reliably removed despite the most intensive rinsing methods. These then escape during the dyeing processes and can then leave “runs” in the visible areas. These are traces where the dyeing is locally destroyed. Sometimes these chemicals also remain after the drying process as unsightly and disturbing crystals. We have developed the patented acidEX® process to optimize the rinsing of such problem areas, but even this does not always provide a satisfactory solution for the most difficult cases. (e.g. M3x15) For components with such situations, we usually recommend sealing these holes with disposable plugs. This is costly, but it gives you a good chance of solving the problem permanently.
This is just a small guide. The whole topic fills volumes, but would go too far here. It is sufficient if you know the basics and we know our way around. Please talk to us. We are always happy to help you with your problems and you can access our expertise without restriction. That’s our job and our hobby!