polymeroxid® LF4®
sondern Low-Friction!
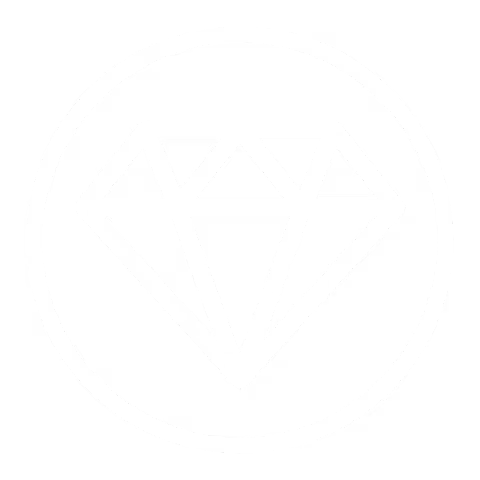
Große Härte
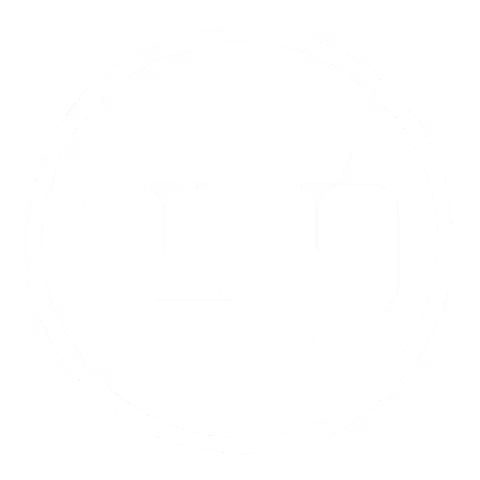
Perfektes Gleitverhalten
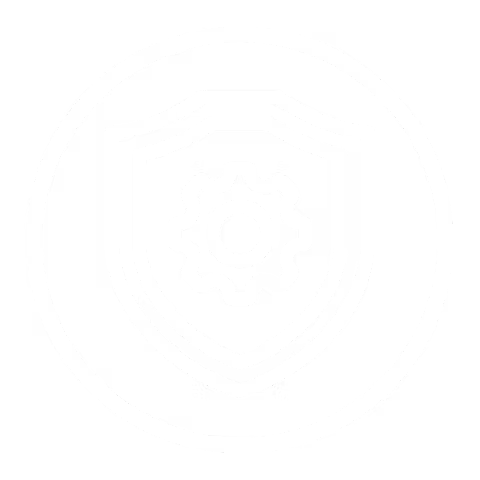
Geringer Verschleiß
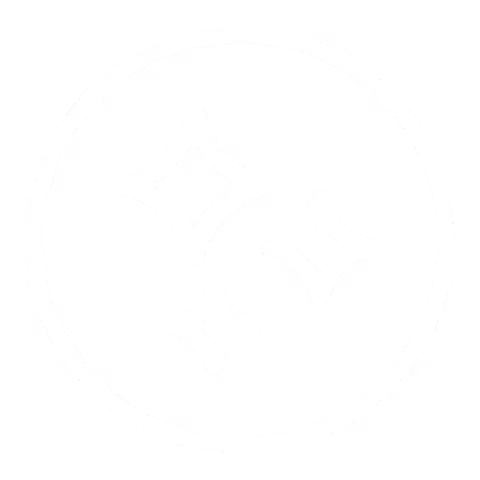
Dekorativ
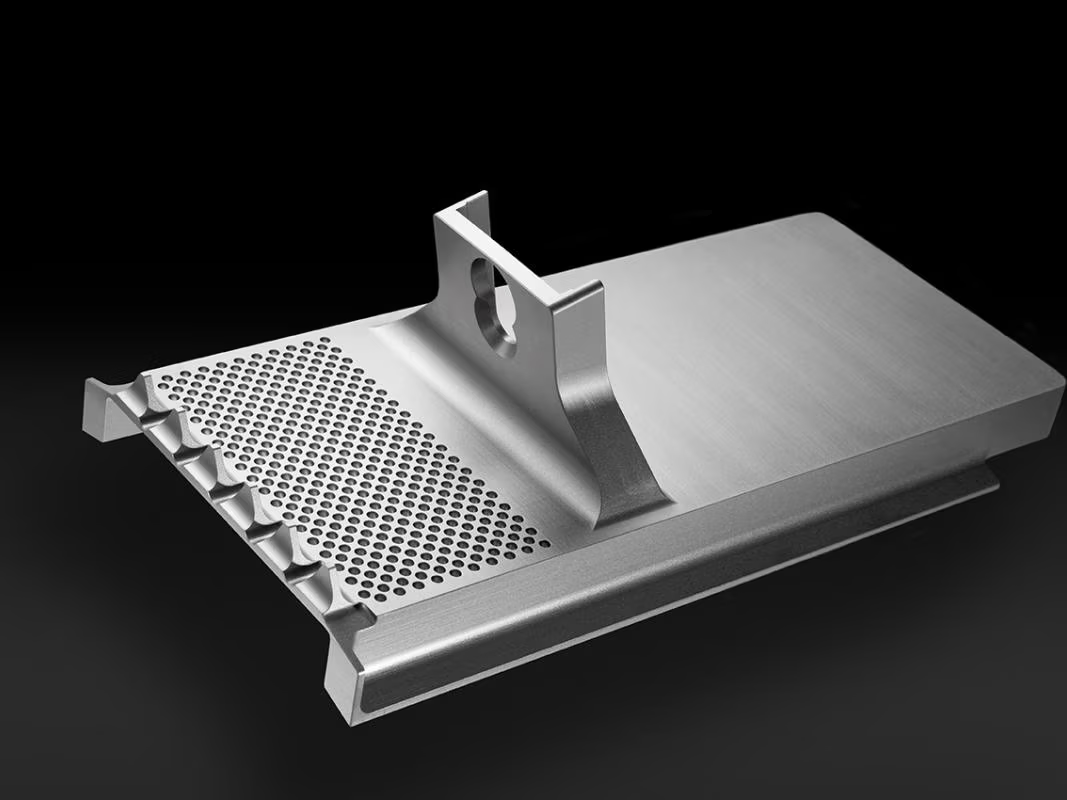
Geboren für den Rennsport
Unser polymeroxid®–LF4-Verfahren ist eine neuartige anodische Spezialbeschichtung für Anwendungen, bei denen die Oberflächen-Glätte im Vordergrund steht. Dazu wurden, bei etwas reduzierter Härte im Vergleich zum xH4®, die Friktionseigenschaften nochmals optimiert. Beim Einsatz geeigneter Werkstoffe ist eine exzellente Dekorativität erzielbar, wodurch sich neue Einsatzmöglichkeiten erschließen, für die das Harteloxieren bisher nicht einsetzbar war.
polymeroxid®–LF4 kommt bei führenden Herstellern von Rennsport-Equipment standardmäßig auf Kolbenlaufbahnen in Dämpfungselementen zum Einsatz. Neben der geforderten Abriebfestigkeit werden bestmögliche Friktionseigenschaften erzielt.
polymeroxid®-LF4 erzeugt die glattesten hartanodischen Schichten auf dem Markt!
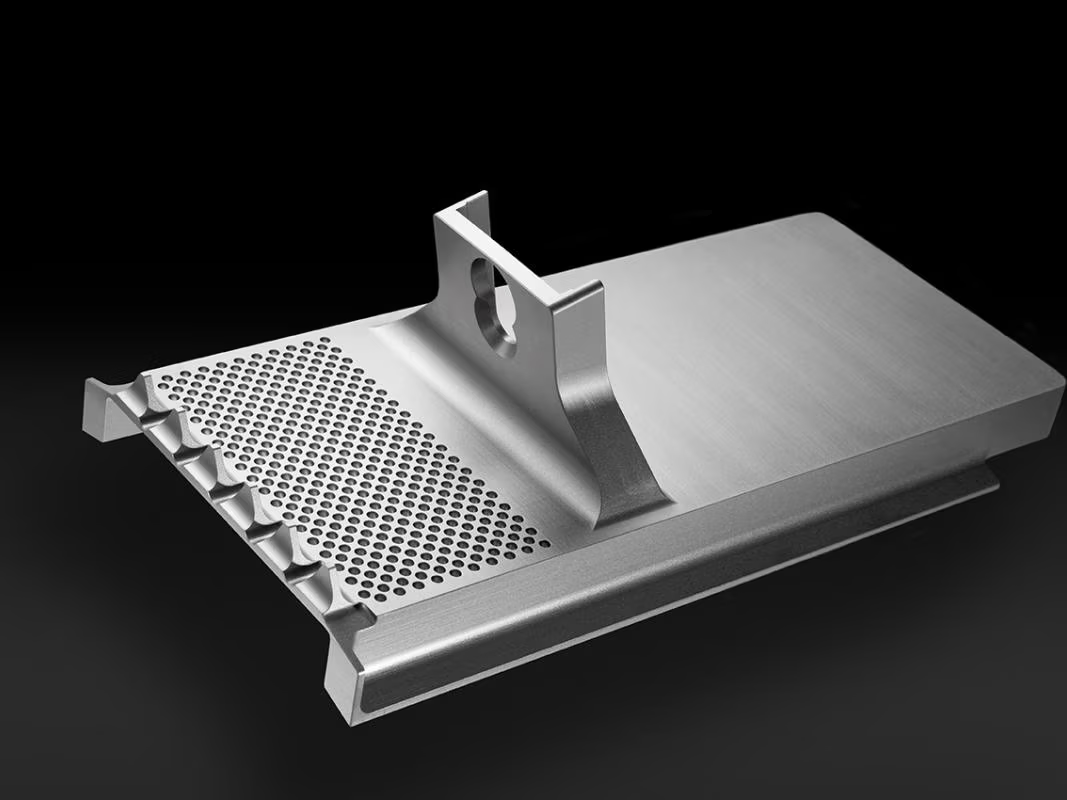
Weil wir es können.
Nur durch die Konstanthaltung aller Prozess- und Badparameter erzielen wir einen nachhaltig hohen Qualitätsstandard. Stetige hausinterne Analytik aller Prozessstufen, PLC-geführte Prozesse, ein eingespieltes Team und unser einzigartiges plano-ERP-System spiegeln sich in größtmöglicher Qualität wieder.
Auch für unsere Eloxal-Beschichtungen führen wir als eines der weltweit wenigen Unternehmen das Typ II-Label des IHAA!
So funktioniert Polymeroxid LF4®
Bei dem neuartigen Verfahren wurden, bei etwas reduzierter Härte im Vergleich zum xH4®, die Friktions-Eigenschaften auf maximale Glattheit optimiert. Hier kann die völlig neuartige polymeroxid®-Matrix die Vorteil ganz ausspielen. LF4 ist das Verfahren der Wahl, wenn es um gleitende Applikationen geht und niedrige Losbrechmomente entscheidend sind.
polymeroxid®-LF4 erzeugt die glattesten hartanodischen Schichten auf dem Markt!

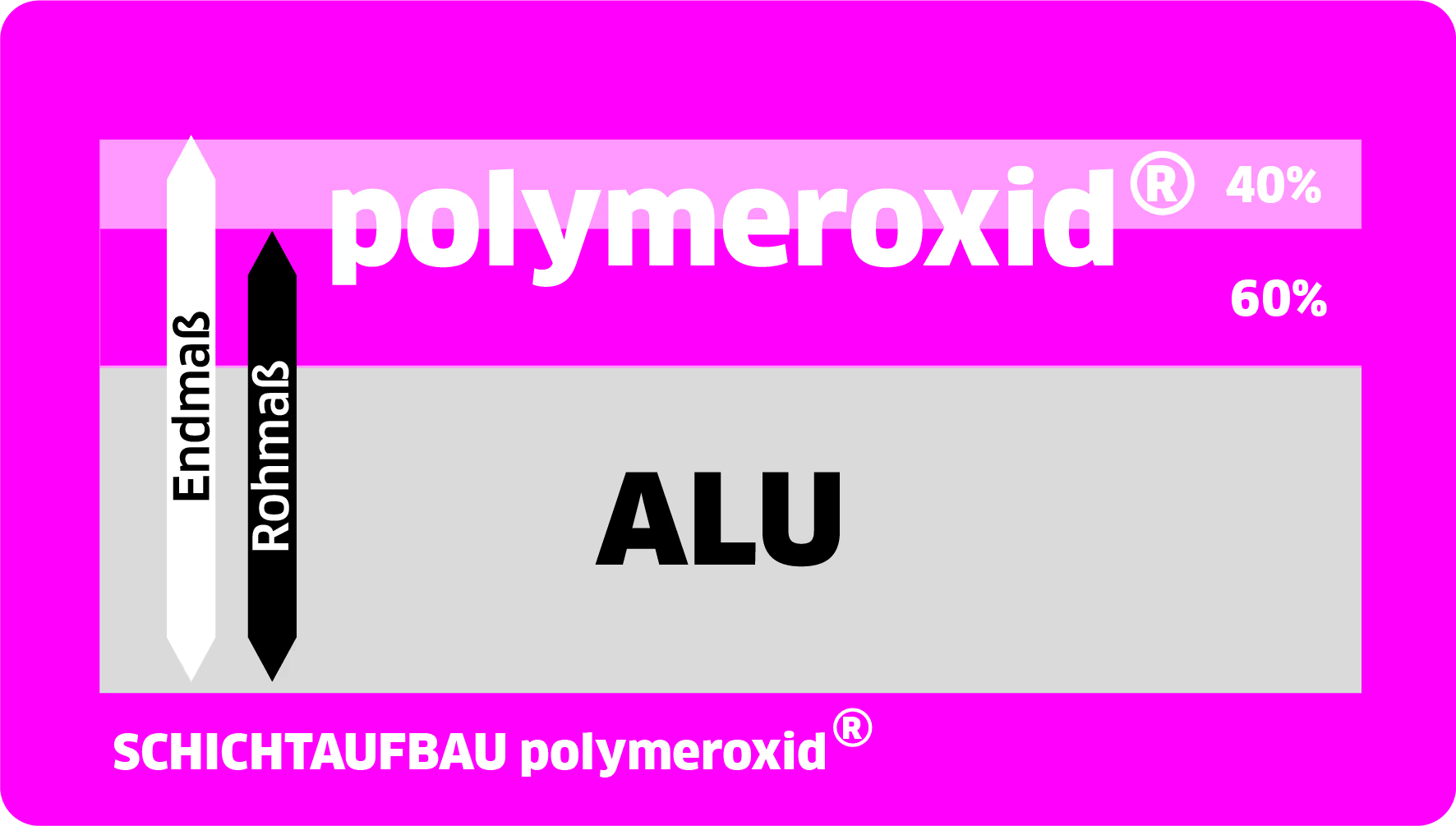
Details:
- völlig neuartige polymeroxid®-Matrix
- glatteste hartanodische Schichten auf dem Markt
- große Härte von ca. 400HV0,25 (7075-T6)
- schützt gegen Kaltverschweißen
- Trotz Harteloxal gute Dekorativität möglich
- sehr große Abriebfestigkeit
- Reduzierung des Slip-Stick-Effektes
- Beste Friktionseigenschaften
- extrem gute Bonding-Eigenschaften mit Top-Coatings
- Werkstoffe:
- Maßverhalten:
- Schichtstärke:
- Schichthärte:
Am besten geeignet sind die Werkstoffe AlZnMgCu1,5 (7075) und AlMgSi0,5/1,0 (6060/6082).
Die polymeroxid®–LF4-Schicht wächst zu 40% ihrer Gesamt-Schichtstärke über die Grundfläche hinaus (siehe Skizze). Eine 25μm Schicht bedeutet also ein Wachstum von ca. 10μm (20µm auf den Durchmesser). Die optimale Schichtstärke liegt zwischen 20 und 25μm.
Schichtstärken <20µm sind technisch nicht sinnvoll. Es haben sich zwei Schichtstärke-Klassen am Markt etabliert. (30 oder 50µm).
Der größte Teil der Werkstücke werden mit einer 30µm-Schicht veredelt.
Warum genau, weniger als 20µm und mehr als 50µm nicht empfehlenswert sind, erklären wir gerne in einem Beratungsgespräch.
Die effektiven Schichthärten sind stark vom verwendeten Werkstoff abhängig. Sie bewegen sich bei unserem LF4 in der Regel oberhalb von 400 MHV0,026 (70765 T6).
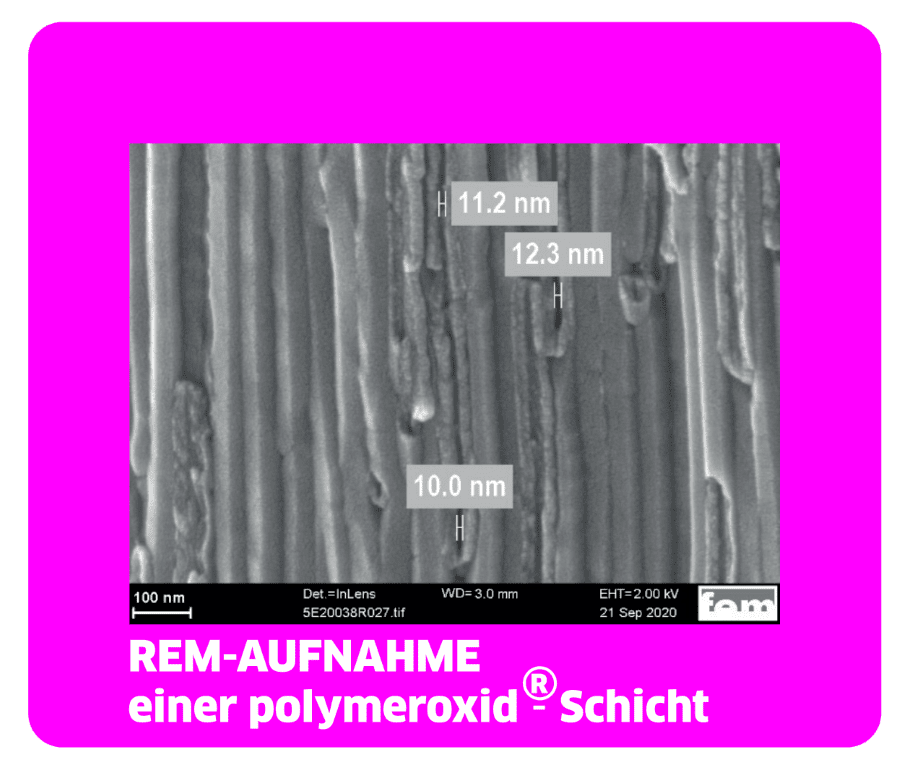
Kostenlose Erstberatung
Dann nehmen Sie Kontakt mit uns auf und profitieren Sie von einer Beratung auf Augenhöhe, ganz ohne Warteschlange. Sie erhalten eine individuelle Beratung und einen festen Ansprechpartner. Durch unsere langjährige Erfahrung unterstützen wir Sie auch gerne in der Planungsphase. Denn wir haben immer einen Plan.
unsere Verfahren
siliseal
Hundertprozentige chemikalienbeständigkeit für LEBENSMITTEL- UND MEDIZINANWENDUNGEN
Laserbeschriftung
Laser-beschriftung
Das garantierte Upgrade in die erste Klasse für Ihr Premium-Produkt